The Comprehensive Guide to Injection Molding of Plastics
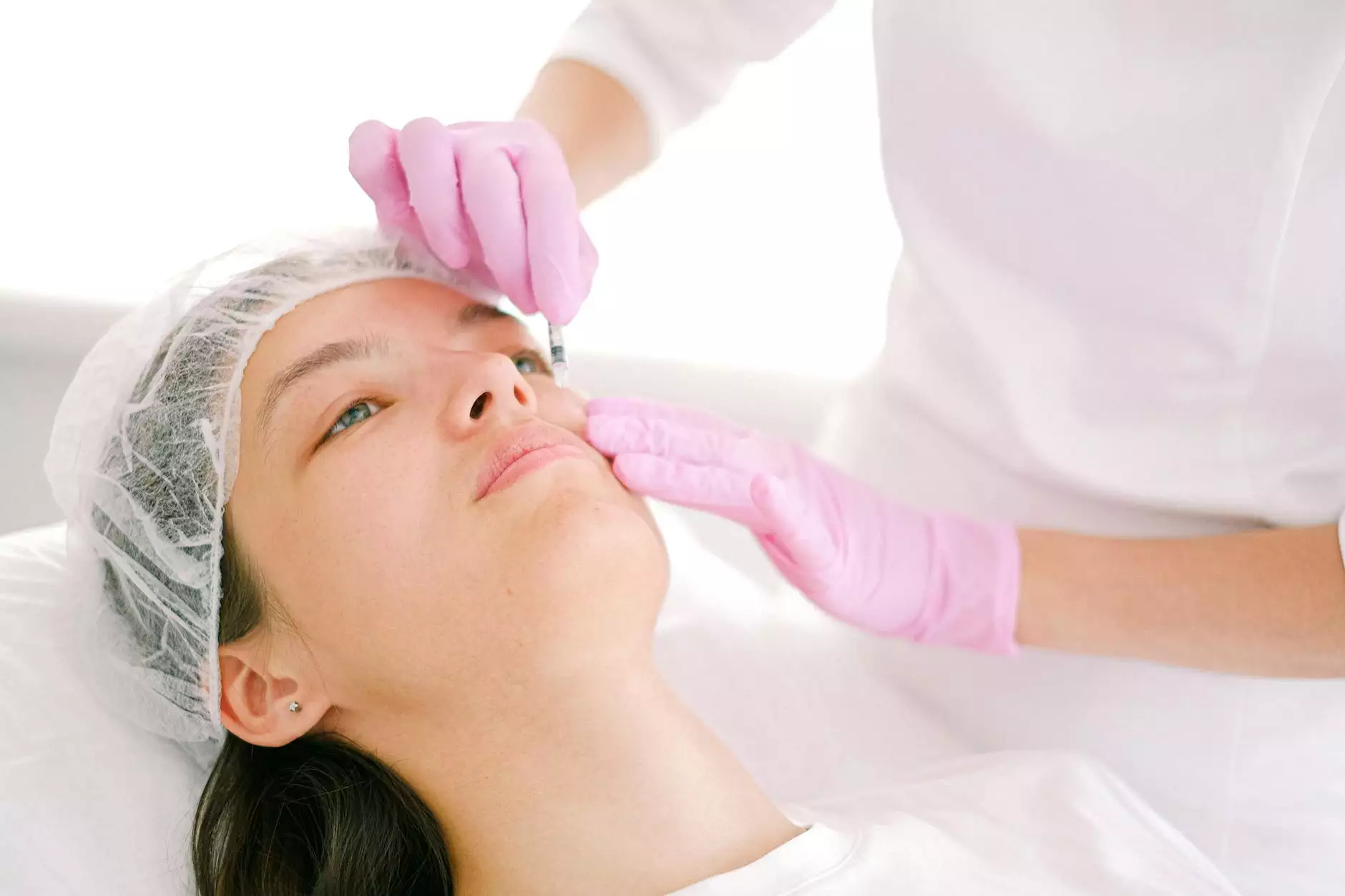
Understanding Injection Molding
The injection molding of plastics is a highly efficient manufacturing process used to create a wide range of plastic components. This method involves injecting molten plastic into a mold, where it cools and solidifies into the desired shape. The process is revered for its ability to produce high-quality, intricate designs with minimal waste, making it an indispensable method in modern manufacturing.
The Process of Injection Molding
The injection molding process can be broken down into several key steps:
- Material Selection: Various plastics can be used, including thermoplastics and thermosetting plastics. Polypropylene and ABS are common choices.
- Melting the Polymer: The selected plastic granules are fed into a heated barrel where they melt into a viscous liquid.
- Injection: The molten plastic is injected into the pre-prepared mold under high pressure.
- Cooling: Once the mold is filled, the material is allowed to cool and solidify.
- Demolding: The cooled components are removed from the mold, completing the cycle.
Advantages of Injection Molding
The injection molding of plastics comes with numerous advantages that make it a preferred choice among manufacturers:
- High Efficiency: Once the mold is designed and built, the production rate is exceptional, allowing thousands of parts to be produced within a day.
- Cost-Effectiveness: For large production runs, the cost per unit decreases significantly, making it more economical.
- Design Flexibility: Injection molds can be engineered to create complex designs that are not feasible with other manufacturing processes.
- Minimal Waste: The precision of the process results in less scrap compared to traditional subtractive manufacturing methods.
- High Quality: The finished products exhibit excellent surface finish and dimensional accuracy.
Applications of Injection Molding
The applications of the injection molding of plastics are abundant, spanning various industries:
1. Automotive Industry
From dashboards to interior components, injection molding produces lightweight, durable parts that enhance fuel efficiency and performance.
2. Consumer Goods
Household items such as containers, toys, and appliances are often made using injection molding due to its versatility and cost-effectiveness.
3. Medical Devices
In the medical field, precision and hygiene are critical. Injection molding meets these needs by producing complex devices that comply with industry standards.
4. Electronics
Many electronic components, including housings and connectors, rely on injection molded plastics for their durability and insulation properties.
Role of Metal Fabricators in Injection Molding
Metal fabricators play a crucial role in the injection molding of plastics. They are responsible for creating the molds that define the shape of the final product. The mold-making process often involves intricate machining and tooling work that requires precision and expertise. Here's how metal fabricators contribute:
- Mold Design: Collaborating closely with engineers and designers to create molds that perform optimally.
- Material Selection: Using high-quality materials such as tool steel to ensure durability and longevity of the molds.
- Precision Machining: Employing CNC machines to fabricate complex mold geometries that meet precise specifications.
- Maintenance and Repair: Offering ongoing support through mold maintenance and repair services to prolong the lifespan of injection molds.
Challenges in Injection Molding
While the benefits are immense, the injection molding of plastics is not without its challenges:
1. High Initial Costs
The cost of designing and building molds can be significant, especially for small production runs. However, this cost is offset by economies of scale in larger productions.
2. Design Limitations
Design complexities may introduce challenges such as warping, shrinkage, and the potential for defects if not carefully managed.
3. Material Limitations
The choice of material can affect the process and final product, necessitating careful selection and testing to ensure compatibility.
Future Trends in Injection Molding
As technology advances, the injection molding of plastics is evolving. Here are some trends to watch:
- 3D Printing Integration: The integration of 3D printing with traditional molding processes can enhance mold design and reduce lead times.
- Smart Manufacturing: The use of IoT devices and analytics in monitoring production efficiency and quality.
- Sustainability: A shift towards biodegradable plastics and recycling processes to minimize environmental impact.
Conclusion
The injection molding of plastics is a cornerstone of modern manufacturing, enabling the production of complex, high-quality plastic parts across various industries. With its numerous advantages, it is no wonder that this process continues to thrive and adapt in a rapidly changing environment. As we look to the future, embracing innovation and sustainability will be essential for companies in the industry, particularly metal fabricators, who play an integral role in this manufacturing revolution. Choosing the right partner in injection molding, like those found at deepmould.net, can significantly impact a business's success in this competitive landscape. By understanding the intricacies and advantages of injection molding, businesses can harness its full potential to drive growth and innovation.